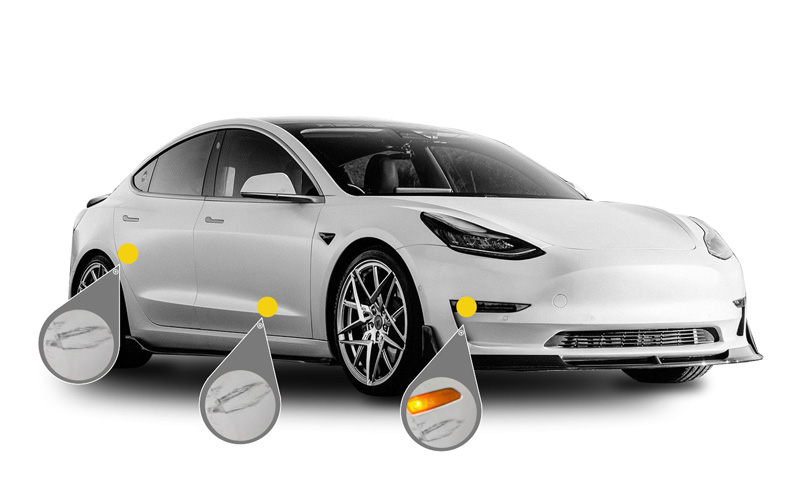
There are different processes aimed at increasing the efficiency and productivity of each repair in the bodyshop and painting sector. One of the most usual types of repair in the daily work carried out at the bodyshop is related to quick repairs, also known as partial repairs or spot repairs.
Reducing working time and material consumption in this type of repair will allow the bodyshop to maximise the profitability of its business, improving the workflow and increasing the opportunity cost.
In this post we are going to focus on providing relevant information about spot repair techniques and efficient processes for small bodywork repairs. Any professional will clearly understand the benefits of integrating these processes in their work methodology.
What is the Spot Repair technique in bodywork?
The spot repair technique is a technique that is used to repair small damages in bodywork, and where the repair area is limited to the area with the defect, not the whole part.
The repair area is limited to the damaged area, not the whole part
It is a repair technique that is aimed at increasing efficiency when repairing small defects. It is based on reducing the working time and repair costs.
When to use the spot repair technique?
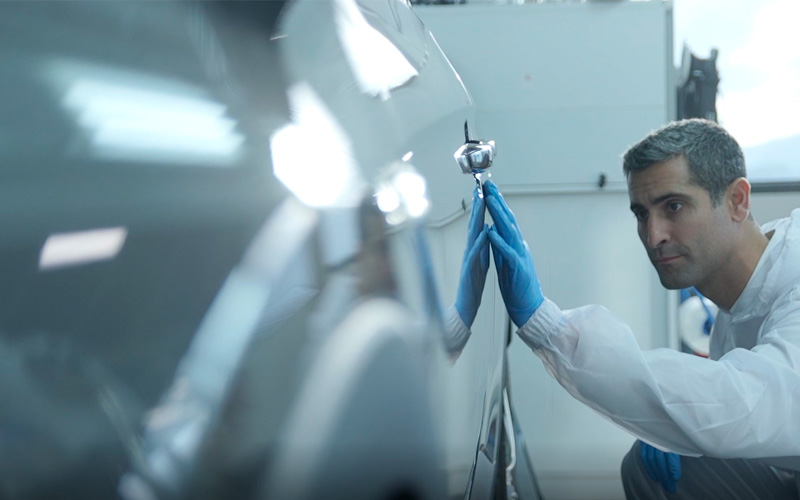
Repairing a car using the spot repair technique in partial repairs will depend on several aspects, which, as professionals, shall be assessed beforehand:
1. Number of parts
Spot repair processes allow repairing parts simultaneously, increasing repair productivity. The number of parts to be repaired can be as many as 3 or 4 parts at a time.
2. Type of finish
The spot repair technique may not be used in some types of finishes, such as matte or textured finishes . This is due to the impossibility of polishing this type of surface, as we would be changing the gloss or texture level, compared to the areas adjacent to the damage. On the other hand, in special colours such as certain metallic or pearlescent colours, it would be more complete to limit the area to repair since a larger surface area would be required for a correct integration of the part.
3. Where is the damage
Except in very specific cases, the spot repair technique should not be used on damage caused to horizontal parts such as roofs, trunks or bonnets because these are highly visible partswhere it is more difficult to conceal the repair. Using the spot repair technique is usual in vertical parts such as doors or wings, and in lower parts of the vehicle, which are very exposed to small friction and scratches, such as bumpers or side mouldings.
4. Condition of the part
Spot repair is recommended in the case of specific, localised damage in certain areas. If the part to repair has on its surface very deep defectsin different locations or colorimetry problems, it may be advisable to use other types of techniques that consider a more comprehensive repair process.
Advantages of using the Spot Repair technique
This technique is specially designed to increase the repair’s productivity and profitability, and the benefits it brings can be manifold:
- Reduction of working time and material consumption: these repairs should be limited to the repair area insofar as possible. It also allows using specific products that reduce drying, preparation and coating time. It also reduces the time used in preparing and masking vehicles.
- Possibility of working with different parts simultaneously, taking advantage of the drying and evaporation times to carry out complementary tasks such as product preparation and mixing.
- Less time spent in the spray booth and less energy consumption, with most of the repair being carried out in areas equipped with suction such as plenums. Vehicle travel times and energy consumption are also reduced.
- Promoting new service and work methodology, without the need for large investments in the bodyshop. Increased repair flow and opportunity cost, which translates into increased profits, productivity and bodyshop competitiveness.
- Better organisation and management of the bodyshop: fast repair services start with a change of mentality and an adaptation of the bodyshop resources, with a differentiated line of work and the necessary resources to meet the delivery deadline. Organisation is also key in this service, minimising non-production times, speeding up the repair process, and accelerating negotiations with the insurance companies.
High Efficiency Spot Repair Process Guide
Processes must be adapted to the type of material we are treating, differentiating between metal or plastic.
Processes must be adapted to the type of material we are treating, differentiating between metal or plastic.
In addition, for a correct prior classification of the repair, a detailed assessment of the damage must be made, assessing whether the damage is superficial or deep, or even if the part must be replaced.
Spot repair processes for damage without deformation
Processes applicable to superficial defects, which do not require a reconstruction of the material:
- Title: DAMAGE WITHOUT DEFORMATION.
- Type of support: Metal and plastic.
- Total time: 90 minutes (depending on the size and number of parts, plus the coating time).
- Description: in this process we will completely repair the paint coats, following the filler, colour and clearcoating phases. To reduce times and optimise product consumption, we will use a quick-drying and excellent sandability filler, such as the PF/7040 in combination with an extra fast hardener. In case of material shortages and bare sheet metal, we will use the SP/7006 spray primer for filling. On the other hand, if there are small areas after the filler, we will use the SPI/7046 primer express filler. Then, we will apply the colour, 1 anchor coat + 1 complete solid colour coat, or 1 anchor coat + 1 complete coat + 1 effect coat in effect colours. The drying will take place in the booth to reduce the drying time of the colour layer. Finally, apply 1 and a half coats of a fast drying clearcoat, such as CC/1770 using a fast hardener (5 minutes drying time with infrared).
- Title: PROCESS WITH SPRAYS.
- Type of support: Metal and plastic.
- Total time: 70 minutes (depending on the size and number of parts, plus the coating time).
- Description: this process is based on a comprehensive use of body sprays to carry out the repair. To do this, we will use a spray on primer (UHS Express Primer SPF/7040), a refillable filler spray for the colour (SPW/4730) and for the clearcoat. This will allow us to significantly reduce repair times, eliminating product preparation and tool cleaning processes, among others.
Spot repair processes for damage with deformation
Processes for small repairs with a deeper damage that require rebuilding the surface.
- Título: D
- Title: DAMAGE WITH DEFORMATION.
- Type of support: Metal and plastic.
- Total time: 110 minutes (depending on the size and number of parts, plus the coating time).
- Description: high efficiency spot repair process, with the same steps as the non-deformation damage process, except for the putty process. Depending on the type of defect, a high quality car putty with excellent filling power, such as the PP/1440 light putty shall be used, to make the coating and sanding processes easier.
Spot repair processes for new part replacement
In newly manufactured parts, we will analyse the repair process to be carried out depending on the nature of the part and its location in the vehicle. To do this, the repair can be carried out through two different processes specially designed to reduce working time and product consumption, while maintaining a high quality finish.
- T
- Title: UNDERHOOD process.
- Type of support: Metal.
- Total time: 45 minutes (depending on the size and number of parts, plus the coating time).
- Description: It is based on the use of the water-based resin WA/6075 UNDERHOOD, specially designed to repair both interior parts (bonnets, door frames, engine compartment, etc.) and exterior bodywork (wings, doors, etc.). Reproduces the original finish in one step. Evaporation time is reduced to 5 minutes.
- Title: WET ON WET process.
- Type of support: Metal.
- Total time: 90 minutes (depending on the size and number of parts, plus the coating time).
- Description: the filler will be used in this process, allowing the surface to be repainted 15-20 minutes after it is applied, without sanding. Designed for coating, even without sanding, new panels with cataphoresis, scratches or minor bodywork damage and as a sealer and integrator of the larger repaired areas. Easy and quick to apply, with a high-quality satin-smooth appearance.
As for the new plastic parts for bodywork, you shall first check if the part has a primer coat or not. Plastic primer, also known as plastic adhesion enhancer, is a product that is mainly intended tooptimise adhesion of subsequent coats of paint, such as putty or filler paint, to the surface.
- Title: Process with a PRIMED PART.
- Type of support: Plastic.
- Total time: 90 minutes (depending on the size and number of parts, plus the coating time).
- Description: in these cases, the part is already primed at the factory. Therefore, we must follow the same procedure as in metal part repairs. You should identify the type of plastic the part is made of, since this will influence the adhesiveness of certain paints. It is important to identify the type of plastic beforehand. If the plastic is compatible with the adhesiveness of the filler to be used, applying an adhesion promoter will not be required.
- Title: Process with an UNPRIMED PART.
- Type of support: Plastic.
- Total time: 105 minutes (depending on the size and number of parts, plus the coating time).
- Description: It could also be the case that the new plastic part lacked a previous primer coat, which would in turn influence the painting process. Professionals shall then need to use an adhesion enhancer or primer for plastic to optimise anchorage in subsequent coats, such as adhesion enhancer PL/1895.
Conclusion
A correct assessment and prior identification of the damage will be the first step to make every small repair in the bodyshop as profitable as possible. As we have seen, integrating cost-effective products and processes for partial repairs into the bodyshop’s working methodology will bring great benefits and advantages to the bodyshop’s income statement.