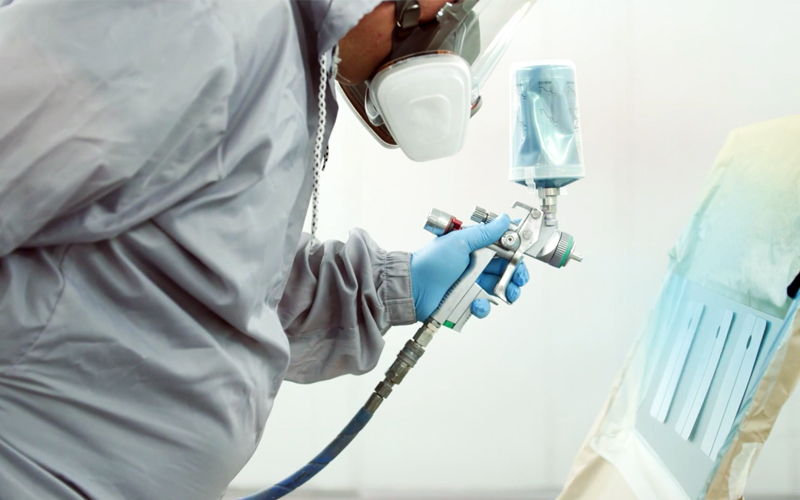
Perfect colour application and colour matching in bodywork depends on different factors and conditions.
Knowing them as a whole, and taking them into account in your work methodology in the bodyshop will help you optimise colorimetry in each repair.
Colorimetry in the bodyshop
Achieving excellent colour matching is one of the most complex tasks for professional bodywork painters.
Video.: How to prevent colour variations.
Leaving aside factors such as the light source or viewing angle, as a professional you have observed on many occasions how applying the same colour mixture on different parts or support can result in slightly different shades.
This is due to the direct influence of several factors that are present throughout the repair process.
The same colour mixture can result in applications with different shades
A clear and precise work methodology will be essential to avoid or mitigate this problem.
Factors influencing the variation of colours
Let us see what are the most important factors that influence the variation of the colour obtained.
1. Distance and position
First of all, the distance and position of the gun are critical aspects to obtain a correct colour.
The greater the distance, the greater the spraying
It is advisable to always keep the same gun distance and its angle with respect to the part.
The greater the distance, the greater the atomisation, resulting in differences in the orientation of metallic particles in metallic or pearlescent colours.
2. Speed
As far as speed is concerned, it is exactly the same. The movement made during spraying should be as even as possible, in order to deposit the same amount of paint on the entire surface to be repaired.
If the speed is too slow, the colour obtained tends to be darker.
3. Spray gun adjustment
The spray gun must be adjusted according to the indications provided in the product’s technical datasheet.
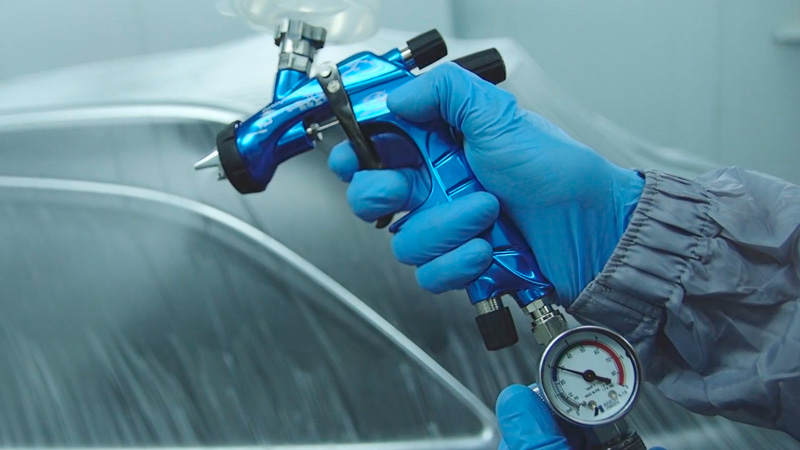
This ensures that we always have a safe and reliable reference.
Low flow and high pressure = lighter shades.
High flow and low pressure = darker shades.
Variations in product flow rate and pressure will also result in variations in colour brightness. Low flow and high pressure, lighter shades. High flow and low pressure, darker shades.
4. Product loading
The product load must be uniform, balancing product consumption, avoiding product excess, to prevent any possible painting defects such as sagging and without applying too light or diluted coats, which would hinder coverage and colorimetry.
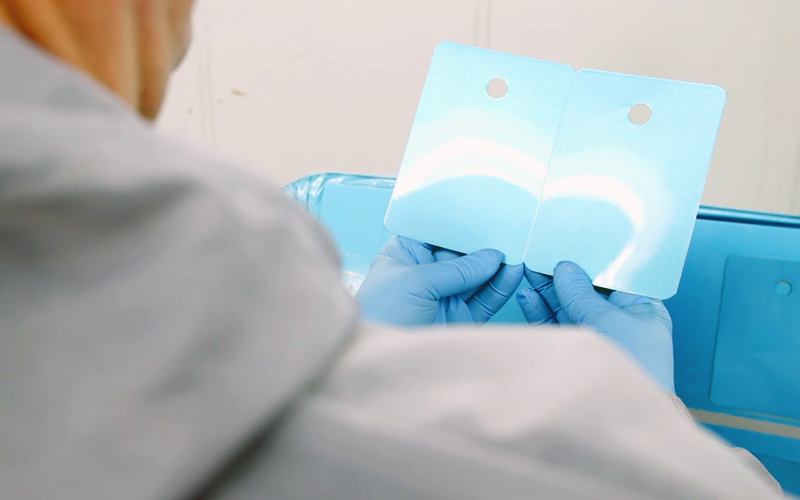
5. Use of thinners
The use of different types of thinners also influences the hue of colour obtained.
The use of fast thinners and excessive thinner in the mixture, will lead to a lighter colour shade, and vice versa.
6. Forcing evaporation
Sometimes we may be tempted to reduce evaporation times by using Venturis or other tools to increase our productivity.
Excessive use of this practice can cause colour variations in the part, which will ultimately lead to colorimetry issues.
7. Temperature
It is important to respect the drying temperature indicated in the product’s technical datasheet, and that both the colour applied in the test tube and in the part should be similar.
Too high a drying temperature may cause the colour shade to become lighter. On the contrary, with a temperature lower than advisable, the colour will acquire a darker hue.
Spray booth airflow can influence variations in the final colour.
In the same way, but the other way round, environmental humidity has an influence. High humidity will darken the colour, and low humidity will lighten it.
In addition, an increasing or decreasing airflow in the spray booth may also result in a slight variation of the final colour.
Working methodology as a key tool to avoid colour variations
As we have seen, the conditions influencing deposition and product behaviour can lead to different colour shades.
In this example, we observe paint test parts painted by the same painter, considering all the factors described above.
We can inevitably observe small nuances when comparing the tests with each other.
To minimise these colour variations, it is essential to follow a clear work methodology, and to have the product’s technical datasheet as an ally.
All this is aimed at increasing the chances of achieving high quality repairs and avoiding rework.