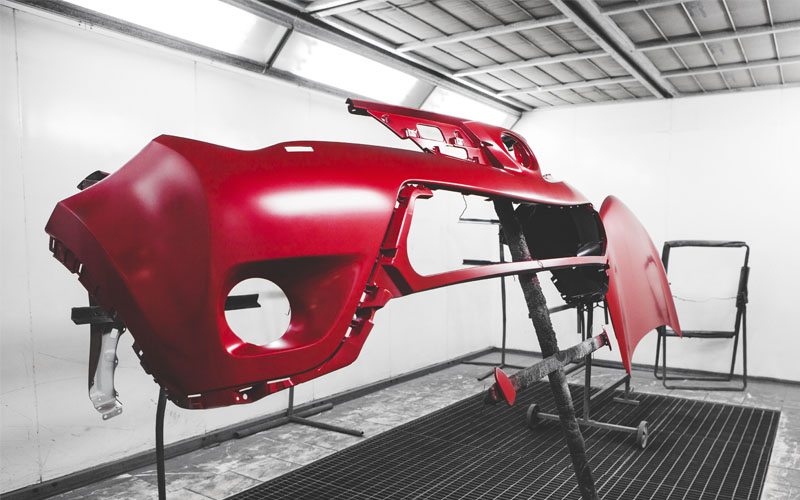
Throughout history, the use of different types of plastics in cars has played a prominent role. However, it is in the last few years, when its use has increased notably due to the appearance of new types of plastics, alloys and composites, offering high performance at a balanced cost.
The continuous innovation of design lines by manufacturers, and the search for efficiency have led to stop using plastic elements for vehicle interiors or auxiliary parts only, and they have becomean indispensable material in various parts of the car’s bodywork such as bumpers, grilles, spoilers, side mouldings or door trims.
Types of car plastics
The emergence of new types of plastics and the improvement of existing ones, in combination with different additives and/or materials (fibreglass) has allowed for their increased use in bodyworks.
Depending on their behaviour at different temperatures, plastics are classified into the following categories.
Thermoplastics
Most of the plastics used in vehicle bodyworks are thermoplastics. This is a type of plastic that it is hard when cold, but that softens when heated, which makes it easier to deform and weld, either by heat or with adhesives.
Their molecular thickness is generally high (composed of linear or branched, non-interlaced macromolecules). The mechanical properties of thermoplastics will vary depending on the mechanical preparation process and its level of polymerisation.
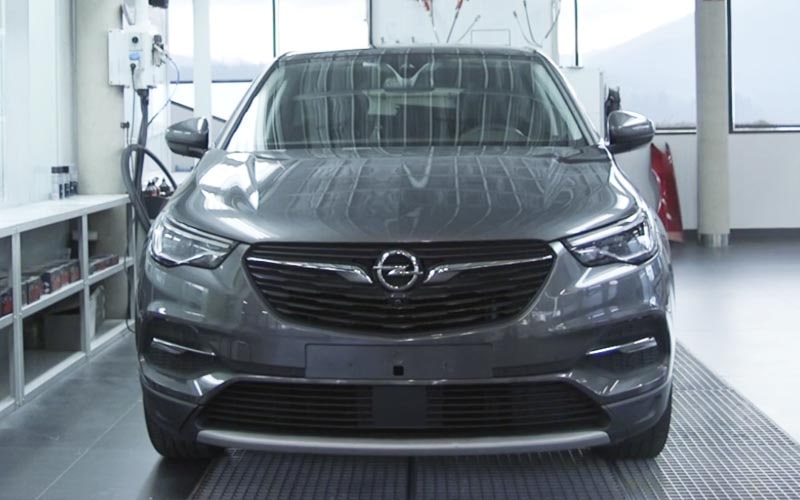
They are plastics that, because of their characteristics, are used for forming parts that must be relatively flexible, aimed at shock absorption and energies caused by small collisions: bumpers, optics, etc.
An added advantage of this type of plastic is that they allow being recycled, enabling and extending their use and life cycle. Let us look at some of the most commonly used thermoplastics:
A.B.S. (Acrylonitrile Butadiene Styrene)
- Characteristics: rigidity and dimensional stability. Provides quality surfaces and good resistance to chemical agents.
- Examples of use: spoilers, grilles, hubcaps, dashboard interiors, etc.
ABS PC (ABS Polycarbonate Alpha)
- Characteristics: greater rigidity and resistance than A.B.S. Also offers good performance in terms of traction and shock absorption.
- Examples of use: grids, spoilers, corner protectors, etc.
PA (Polyamide)
- Characteristics: is a plastic that is resistant to impact, to wear and to a wide variety of chemicals. It allows the use of different densities to make it more flexible or more rigid according to needs.
- Examples of use: grids, hubcaps, interior lining.
PC (Polycarbonates)
- Characteristics: great rigidity and hardness, and very resistant to impact. Good resistance to weathering and are easier to repair than other types of plastic (good performance for painting and welding). Capable of withstanding temperatures of up to 120°C
- Examples of use: spoilers and corner protectors, grilles, bumpers, etc.
PE (Polyethylene)
- Characteristics: one of the most widespread polymers. highly elastic on impact and easy to recover their original shape. Great performance against heat and a wide variety of chemical agents. Used also in the production of electrical components. They can begin to deform from 87°C.
- Examples of use: ducts, batteries, wheel arch liners, bumpers, etc.
PP (Polypropylene)
- Characteristics: it is one of the most widely used plastic materials in the automotive industry for different parts and components. Its performance is very similar to “Poliepileno”, although with better performance against traction, shock absorption and heat (up to 130°C). It also provides great elasticity and rigidity, and good performance against chemical agents.
- Examples of use: ducts, batteries, wheel arch liners, bumpers, etc.
PP – EPDM (Ethylene Propylene Diene Monomer)
- Characteristics: is an elastic and resistant plastic, with a great structure recovery after impact, greater than that of Polypropylene. It is resistant to most solvents and acids, and to high temperatures.
- Examples of use: bumpers, interior or exterior coatings, spoilers and flaps, etc.
PVC (Polyvinyl Chloride)
- Characteristics: in combination with different types of additives, it offers a wide variety of results, such as high-flexibility structures and other rigid ones. They are resistant to moisture, acids and solvents and to wear and tear, but not to high temperatures. Easy application of colour on its surface.
- Examples of use: electrical cables, bus floors, etc.
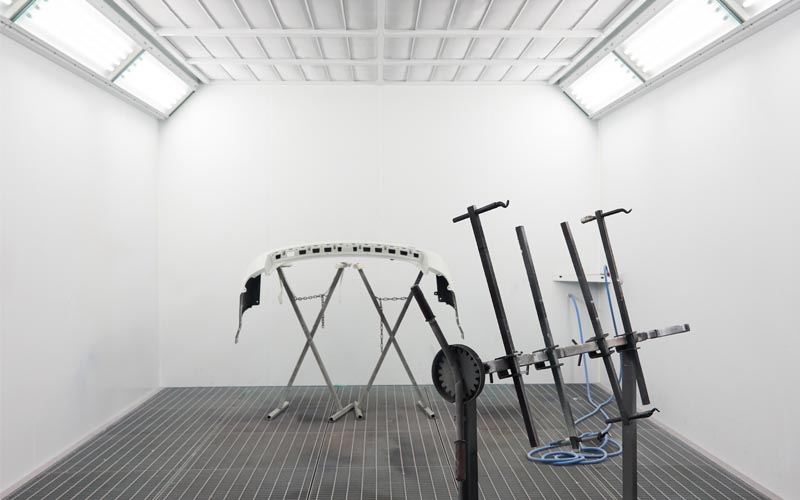
Thermosets
They are composed of chains of linear or branched molecules joined together to form a network that provides hardness and rigidity.
They are called like this because do not get deformed when subjected to heat, mechanical pressure or certain chemicals, always maintaining their original structure.
Unlike thermoplastics, an excessive application of heat will not cause it to deform but will result in decomposition or charring of the heated area, without altering its shape.
Therefore, they cannot be welded, but they can be repaired with other techniques, such as adhesives or resins.
Its features include high mechanical resistance and rigidity. They are mainly used on parts that will not be subjected to bending or that can withstand high temperatures, such as crankcase covers or radiator supports.
The most commonly used thermosets in the automotive industry are unsaturated polyester resins such as epoxy resins (EP) and polyurethanes (PU, usually reinforced with mineral or synthetic fillers to increase the mechanical properties of these plastics).
GU-P / BMC-SMC-MMC (Glass Reinforced Polyester Resins)
- Characteristics: these are plastics that stand out above all for their lightness and rigidity, while offering good mechanical performance.
- Examples of use: gates, hoods, grids, isotherms, channelling, etc.
EP (Epoxy Resin)
- Characteristics: they offer variety in terms of stiffness and elasticity performance. They can be reinforced with loads and fibres. Good adhesion on other plastics, with the exception of olefinics (PE, PP). Resistant to corrosion and chemical agents.
- Examples of use: modification of bodywork parts such as skirts, bumpers, heel cups, spoilers, etc.
GFRP (Glass Fibre Reinforced Plastics)
- Characteristics: they are very hard and resistant. They incorporate glass fibres and thermosetting resins (polyesters, epoxies, etc.). They cannot be welded, but they can be repaired.
- Examples of use: bumpers, dashboards, etc.
Elastomers
The main characteristic of elastomers is that they are highly flexible and elastic. When faced with external pressure, they tend to deform, recovering their original shape when the pressure ceases.
Once broken, they are more difficult to repair. These plastics are repaired by using adhesives, as they cannot be welded since they degrade when excessive heat is applied.
Most elastomers are composed of versions of rubber, such as thermoplastic polyurethane (PU or PUR if reinforced), ethylene-propylene-diene (EPDM) or styrene-butadiene (SBR).
In the automotive industry, elastomers are mainly used for parts such as spoilers, gaskets or rubber for windows.
Methods for identifying the type of plastic in the bodywork
Due to the rapid evolution of these components in the sector, it is essential that professionals know in depth the different types of plastic that make up a car, their behaviour, and the ideal repair processes to obtain an optimal result and reproduction.
Not in vain, at present, plastic is used in vehicles around 18% in a mid-size model. This figure is expected to increase further in the future.
Knowing in depth the different types of plastic used in the automotive industry will help to optimise their repair. Let us now look at some methods for correct identification
Identification code
Today, we can identify the plastic parts of a vehicle through a kind of number plate or identification code located inside, which specifies the exact composition of the part (type of material and reinforcement load if any).

This information is delimited by the symbols “>” and “<“. Other information such as the month and year when the part was manufactured can be found.
Contrary to what one may think, this information is collected to make their recycling process easier, and not to provide additional data in the repair.
Organoleptic analysis
This consists in carrying out a series of subjective tests by applying a fire flame to the plastic in order to determine the type:
Flame behaviour | Flame colour | Smoke | Characteristics | Possible plastic |
---|---|---|---|---|
Somewhat intense flame. It goes out when the flame is removed. | Green | PVC | ||
Yellow | Not much | It melts. | PUR | |
A lot | It melts, carbonises and makes bubbles | PC | ||
It still burns when the flame is removed. | Bluish or white blue | Smokeless | It melts and the combustion zone becomes transparent | PE |
It melts and the combustion zone becomes transparent. Threads are formed by stretching the melted part. | PP | |||
It melts and drips | PA | |||
Yellow | Black and dense | It is fragile | PS | |
The break area is whitish | ABS | |||
It melts, bubbles and chars | ABS/PC |
Advantages and disadvantages of the use of plastic in bodywork
The performance of plastic in the automotive industry gives them a clear advantage over other materials such as steel or aluminium, due to their lower weight and cost, better adaptation to environmental regulations or the possibility of being recycled.
Advantages over other materials
The increasing presence of plastic in the bodywork of vehicles is due to a series of advantages that are difficult to achieve with other types of materials:
- Less weight: the increase in the size of vehicles and the increase in the number of parts used in their manufacture make it essential to use materials that help to reduce the total weight of the vehicle. Without plastic parts, today’s vehicles would be between 180 and 300 kg heavier.
- Reduction in consumption: this reduction in weight also leads to a reduction in consumption, resulting in savings of around 0.5 litres per 100 km.
- Environmental impact: lower consumption in turn leads to a reduction in emissions, an essential aspect today to comply with current regulations. In addition, it is a material that can be recycled, extending its useful life.
- More complex design lines: These allow the design of panels with complex geometries, which also influences the dynamic performance of the bodywork.
- Good thermal, electrical and acoustic insulation performance: This enables running comfort and better shock absorption at low speed because of their greater flexibility.
- No rusting.
- Reduction of cost and time in the assembly process.
Disadvantages of the use of plastic
Despite bringing many positive aspects to a vehicle body, plastic parts can have some drawbacks:
- Less resistant to weathering: prolonged exposure to the weather can cause degradation of the material, resulting in a loss of gloss and strength of the exposed plastic.
- Increased sensitivity to chemical agents: some plastics have a lower chemical resistance to some products such as solvents, which can damage the plastic substrate.
- Less adherence and incompatibility with some paints: due to the features of certain plastics, it is advisable to use specific paints to ensure better adhesion.
Conclusion
The rapid evolution of bodywork plastics require continuous updating by professionals. Knowing the different types of plastic that exist and the methods to consider for their correct identification will allow professionals to adapt each repair to the ideal painting process, improving the workshop’s profitability and productivity.