SINNEK WS/6314
TRANSPARENT RED
Simplifies the reproduction of complex three-coat colors
Introducing an innovative product specially designed to make it easier to reproduce complex colors such as MAZDA’s Soul Crystal Red 46V and Soul Red 41V or Ford’s Europe RubyRed.
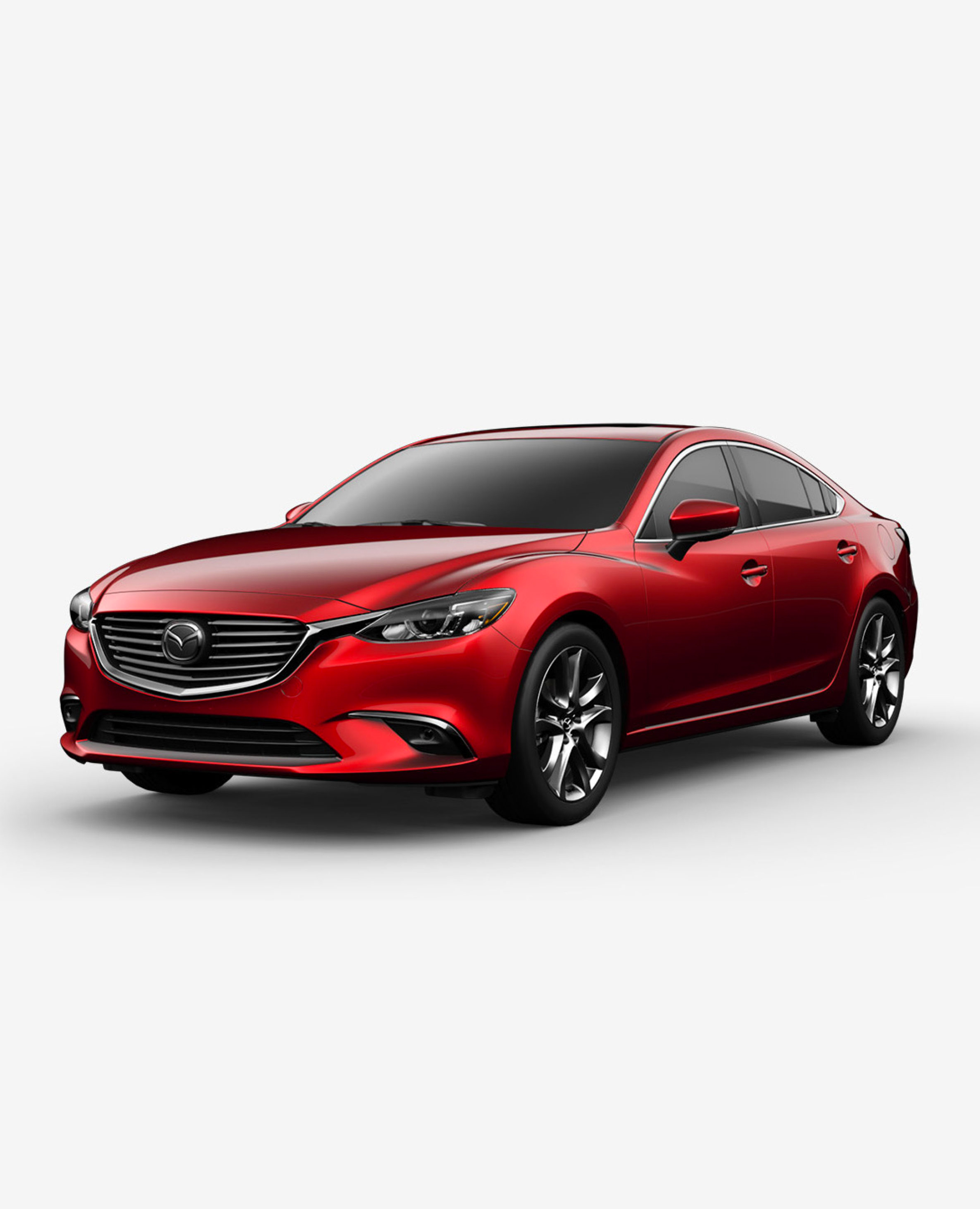
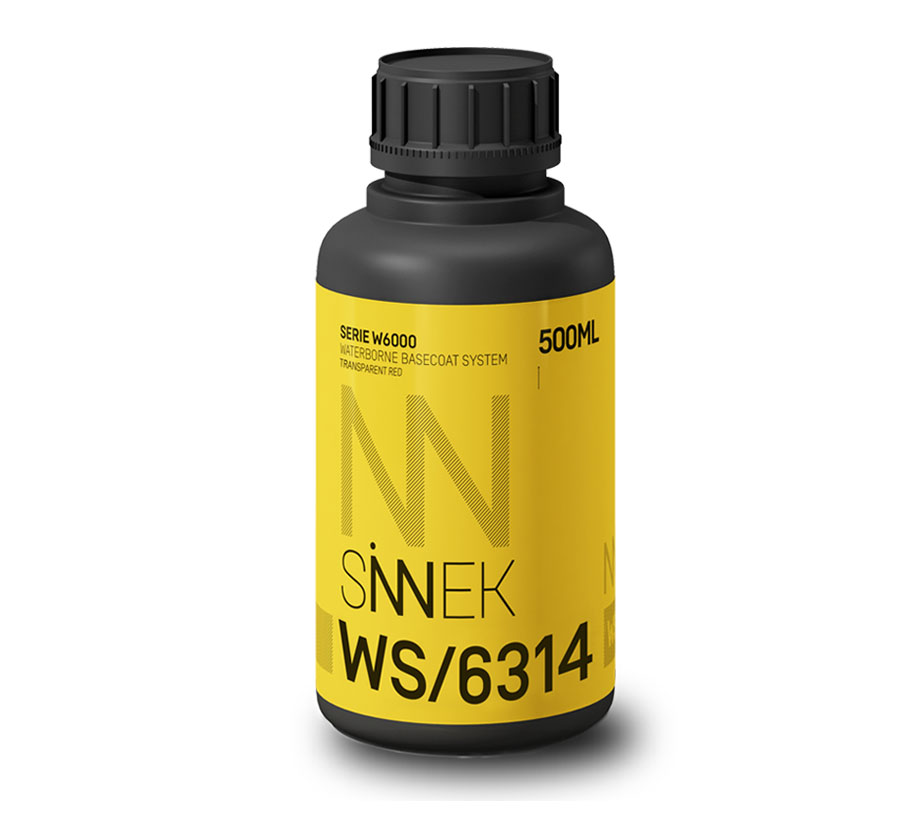
Excellent color matching in a fast and easy way
By using the basic WS/6314 Transparent Red, we convert a complex color process into a regular three-coat color.
This basic is included in the W6000 Series waterborne system by SINNEK, which will make us be more agile and productive, in addition to make us save costs notably, reducing the repair process by more than half.
It also allows professionals reproduce these complex three-coat colors, without the need to apply an intermediate coat of dyed varnish.
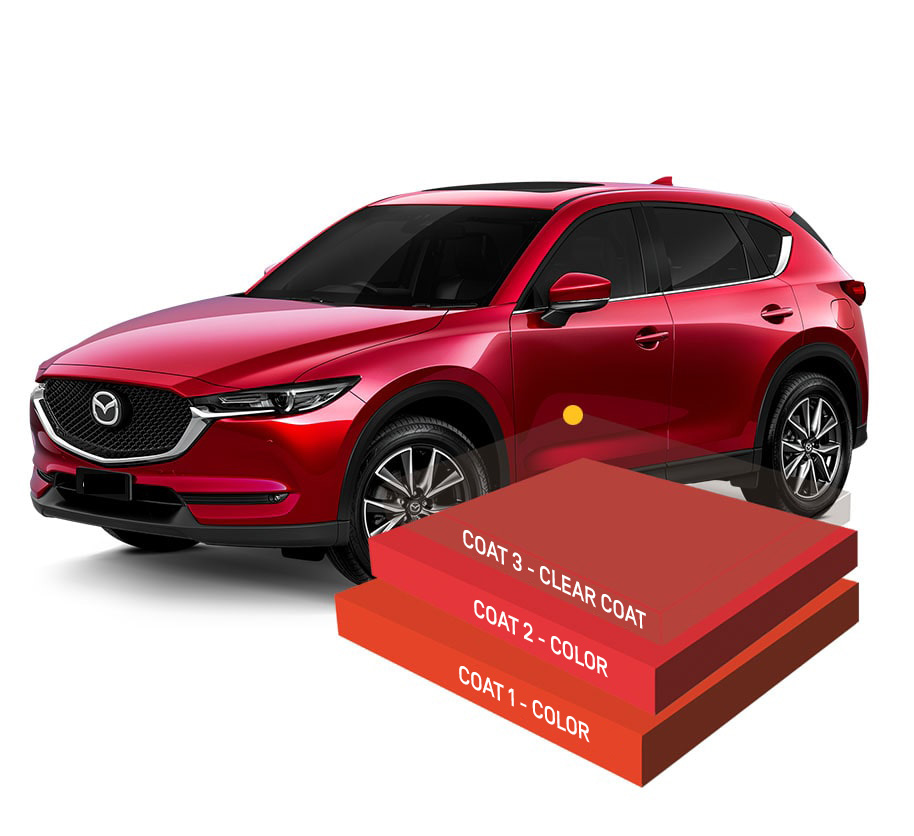
Advantages of Use
The use of the WS/6314, a waterborne basic, has a number of advantages over other processes in the sector:
- It simplifies and speeds up the repair of complex colors as it is integrated within the W6000 Series waterborne system.
- It saves repair time and increases productivity.
- It reduces costs and material used by more than half compared to other processes on the market.
- There is no need to apply an intermediate coat of died varnish.
- It contributes excellent depth, vividness and color matching.
- It makes it easier to perform blurring effects.
- Excellent strength and resistance to sunlight and bad weather.
Application process
Using SINNEK's basic WS/6314 will simplify the repair steps, reducing time and costs compared to other processes on the market.
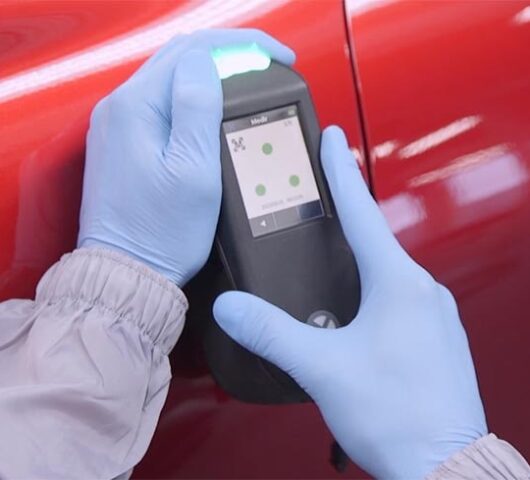
Previous Steps
First, use the spectrophotometer to get an accurate color reading. Measure the adjacent area to optimise the integration of the part in the bodywork.
Choose the color of the tackle based on the indications of SINNEK’s color software, in order to obtain a correct opacity and coverage.
Subsequently, prepare 3 test tubes to optimise the color matching of the part.
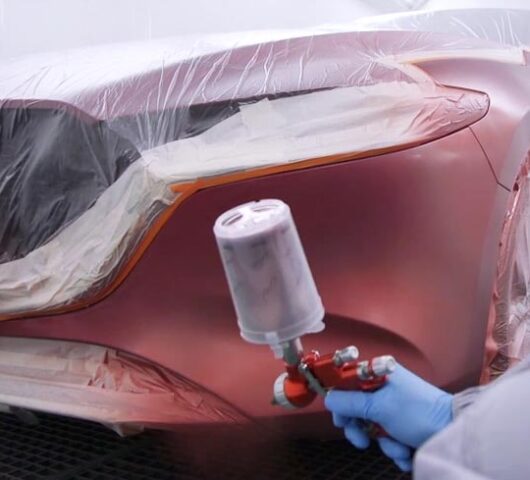
Coat 1 - Color
Formulate the color of the first coat with a dilution between 15 and 25%. Add 5% activator to the mix.
- Apply a first fine coat as contact or anchor.
- A second, more even, extended and regular coat over the entire surface, avoiding overloading the edges.
- Finally, a control coat , which will help us to correctly position the metallic particles of the color.
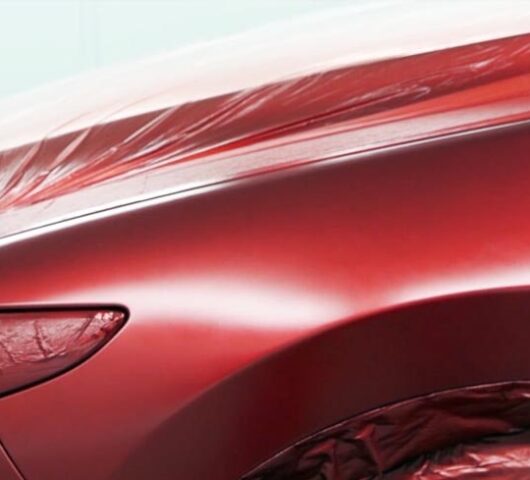
Coat 2 - Color
This second coat will provide brightness and depth to the color, allowing light to pass through and be reflected on the metallic particles.Mixtures are diluted between 25 and 35%.
- Apply the number of coats established based on the previously conducted test runs.
By using a waterborne system, we avoid the shadows that are produced on the edges of the part, and we can also shorten evaporation times with a Venturi.
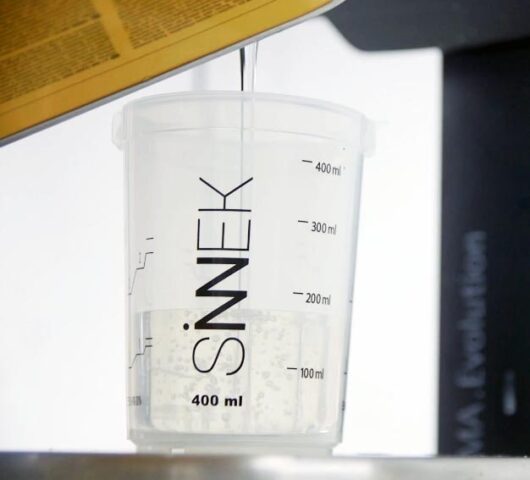
Coat 3 - Clear coat
Finally, the Clear coat coat is applied.
Apply two regular and even coats over the entire surface.
In this way, we provide extra chemical and mechanical resistance to the surface and prevent the coat of clear coat from copying the base structure, preventing any possible painting defects.
HIGH PRODUCTIVITY
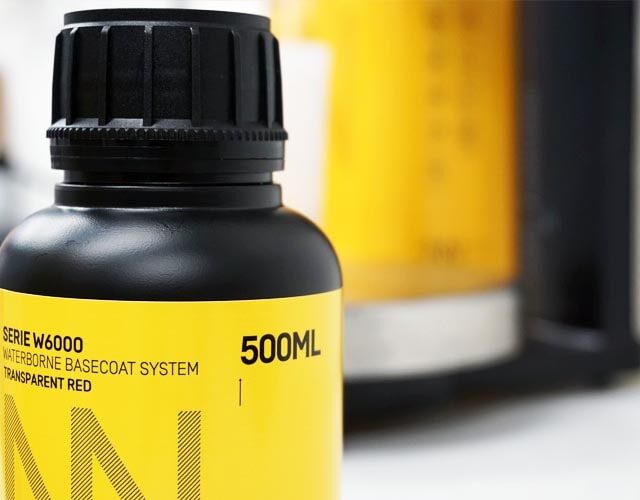
COST REDUCTION
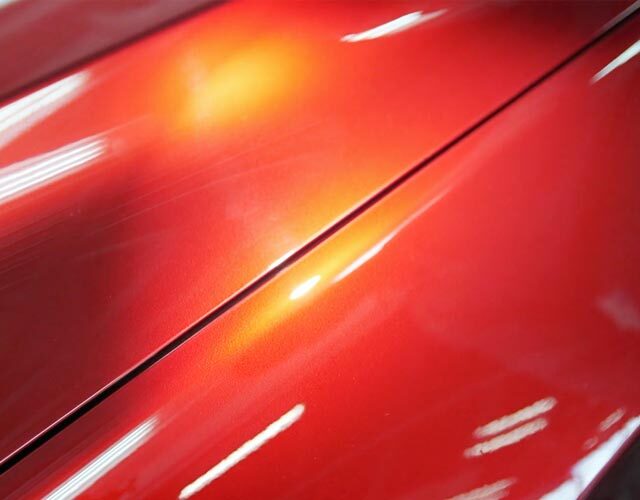
EXCELLENT COLOR MATCHING
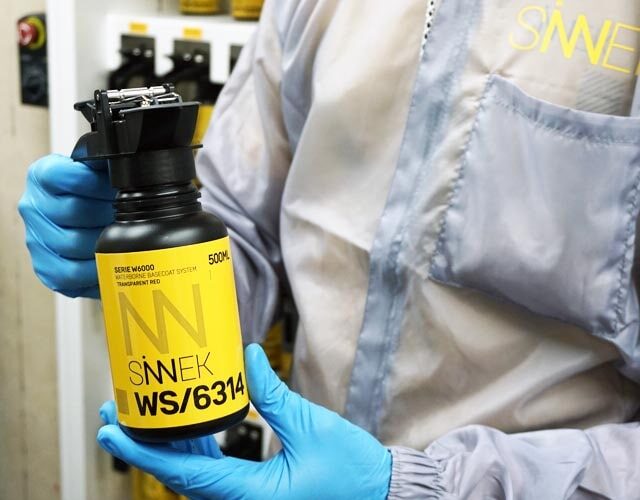
AGILITY AND SIMPLICITY